Higher building standards and renewable electricity generation are also leading to reductions in CO2 emissions from the day-to-day, operational energy used in buildings. However, construction industry stakeholders are increasingly focused on reducing embodied carbon as a critical issue in delivering a decarbonised built environment.
As a result, embodied carbon from construction and the materials it uses makes up a higher proportion of buildings’ whole life carbon emissions. The World Green Building Council estimated in 2019 that “carbon emissions released before the building or infrastructure begins to be used will be responsible for half of the entire carbon footprint of new construction between now and 2050.”
Portland cement is a carbon intensive material which, although acknowledged as a major source of carbon dioxide when used in concrete, is vital to the construction of many new buildings and infrastructure assets.
BRE’s Andrew Dunster and Elsabeth Marriot recently published the paper “Lower carbon dioxide cements and concretes: Bringing new materials into UK industrial use” in a special issue of Proceedings of the Institution of Civil Engineers Structures and Buildings journal.
Cement manufacture is responsible for around 7-8% of global CO2 emissions with significant growth in the global industry anticipated over coming decades. Beyond efficiencies in cement manufacturing and strategies to use less cement in construction, a further option is to move towards cements with different compositions and inherently lower embodied carbon.
BRE’s paper in Structures and Buildings focuses on these materials, their use in concrete, and addressing the barriers and challenges to their widespread adoption; it draws mainly on applied research, manufacturing and site trials and standardisation activities conducted within the UK and EU.
The paper describes the role of standards/specifications and their underpinning information (such as applied research, published case studies and experience) which is essential in getting any new cement adopted.
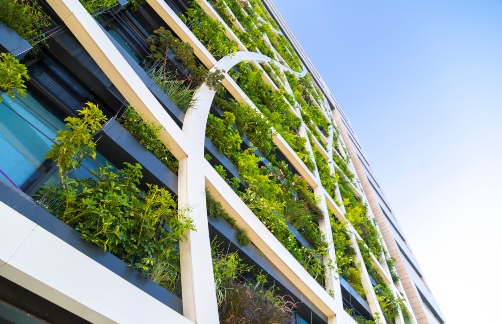
In addition to the modification of standards, provision of basic and specific technical and practical information such as strength development curves, durability, site considerations and a shared broad body of evidence are needed before specifiers can begin to consider using any new cement. BRE is well equipped to carry out independent assessments of structural performance and long-term durability, and act as an independent holder of performance data.
The paper calls for clients and specifiers to:
- Avoid over-prescriptive specifications that restrict the concrete supplier’s choice of materials un-necessarily.
- Work more collaboratively with concrete suppliers enabling them to provide/offer a solution to performance and service life requirements at the lowest embodied CO2.
Recommendations
- Support for more structured and specific R&D programmes, specifically including the collaboration of a supply chain-orientated consortium with other interested parties including industry, research organisations and academia.
- Initiation of durability work on new cement systems (under relevant conditions) without delay to generate long term data.
- Industry or government funding to resource the continuation of long-term monitoring of emplaced concrete test specimens or trial elements, to support implementation of findings and outcomes through standards or sharing of pre-competitive know-how and data.
- Establishing a suitable forum for open-source sharing of research and test data on new materials to minimise duplication of effort across the industry and maximise the opportunity for uptake.
Low risk field and production trials of concrete elements or pours can provide an opportunity to test binder technologies at realistic scale and establish compatibility with established production processes.
Gradually introducing these materials in non-working structural elements or applications such as roof tiles or pavers can enable producers/clients to gain familiarity with a new cement system before introducing it into reinforced and/or more critical structural elements.
Performance of concrete elements can also be evaluated over time in realistic service environments if trial sites with long term access can be arranged. Data-rich case studies demonstrating cost-effectiveness, successful field trials and any other benefits can then be deployed to persuade clients of the advantages of these lower carbon materials.
Find out more about BRE’s concrete testing services.